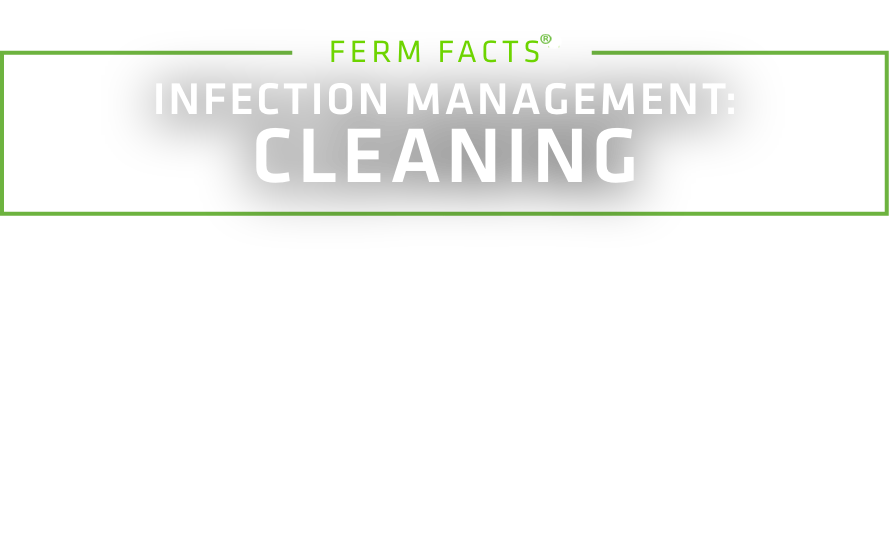
Infection Management: Cleaning
The most important defense against bacterial infections is proper sanitation of plant equipment. Uncontrolled bacterial growth can cause plant maintenance issues, reduced efficiency and productivity, increased operational costs, and diminished profits.
The most optimal area for bacterial growth is plant heat exchangers. They provide ideal conditions for bacterial proliferation as a result of:
- A restricted pathway that is difficult to clean
- An abundance of surface area on exchanger plates where bacteria can grow
- The presence of sticky mash that contains a food source as sugars and starches break down
More specifically, front-end heat exchangers after liquefaction but before fermentation are often transferring mash that has not been treated with an antimicrobial. Although infections are most common in heat exchangers, all process areas need to be monitored and cleaned regularly to prevent bacterial growth and maintain healthy fermentations. Mash fill and transfer lines can also be problematic if not sufficiently cleaned. Some of the additional process areas to monitor include plant storage tanks, piping dead legs, grain bins, and propagator air spargers or eductors (Figure 1).
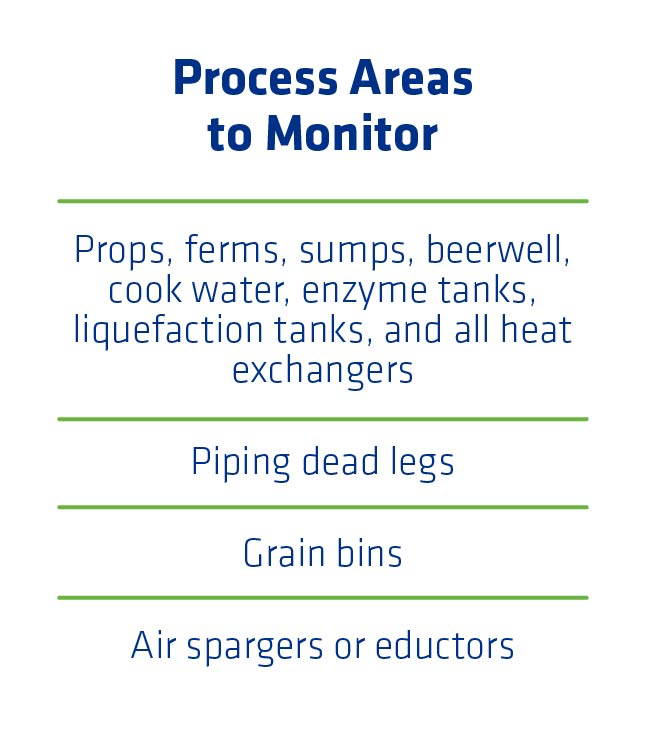
Impact of Dead Legs
The risk of incomplete fermentation increases when bacterial levels reach a certain threshold (and above). This threshold is 105 colony-forming units per milliliter (CFU/ml) and plants need to take corrective action to prevent problems with fermentation when this bacterial level is reached.
Bacterial counts can increase to 105 CFU/ml if just one gallon of mash infected at 108 CFU/ml mixes with 1,000 gallons of clean mash. This could happen if one gallon of mash sits in a dead leg or some other contaminated spot (i.e. heat exchangers). Considering that bacteria can double every 20 minutes and have growth rate 5 to 8 times faster than yeast, a large scale infection can happen quickly. See Figure 2 below for an illustration of the impact of a small dead leg on Lactic Acid Bacteria (LAB) counts.
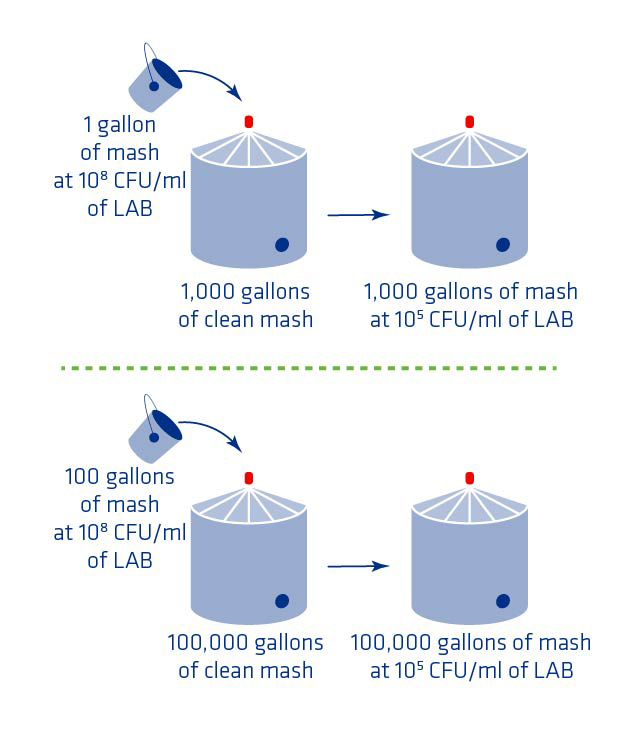
Biofilms Make Cleaning Difficult
Biofilms are another potential problem area for ethanol plants. They can start as a small cluster of bacteria. As the bacteria grow and replicate, a slimy substance comprised of polysaccharides, proteins, and DNA is excreted. This slimy matrix protects bacteria and allows survival in more adverse conditions, including chemical cleaning.
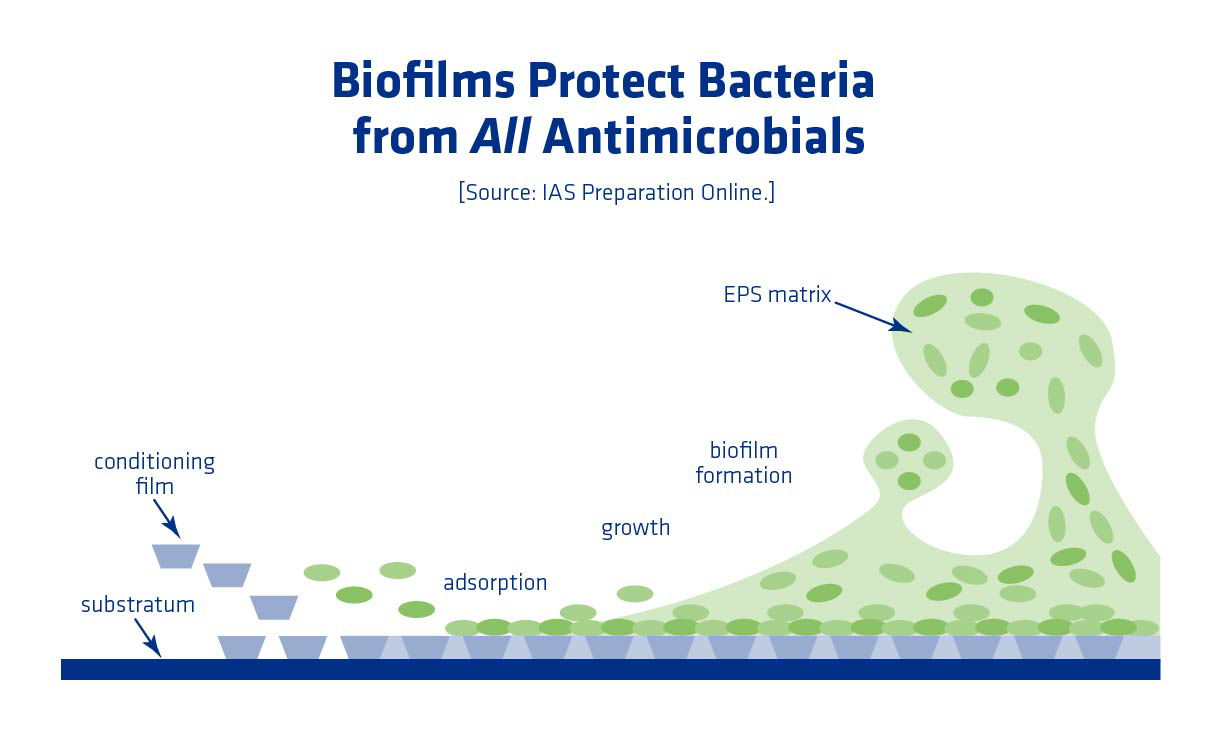
Combating biofilms can be difficult. Clean In Place (CIP) can erode some of the biofilm outside layer, but it can’t penetrate enough to kill all of the bacteria. Using heat is also often ineffective because the slimy matrix insulates the bacteria, allowing survival at higher than normal temperatures. The bacteria in a biofilm matrix are typically less metabolically active in comparison to normal vegetative cells, and therefore less sensitive to antimicrobials. In addition, biofilms are affixed to a surface and can’t be easily flushed away.
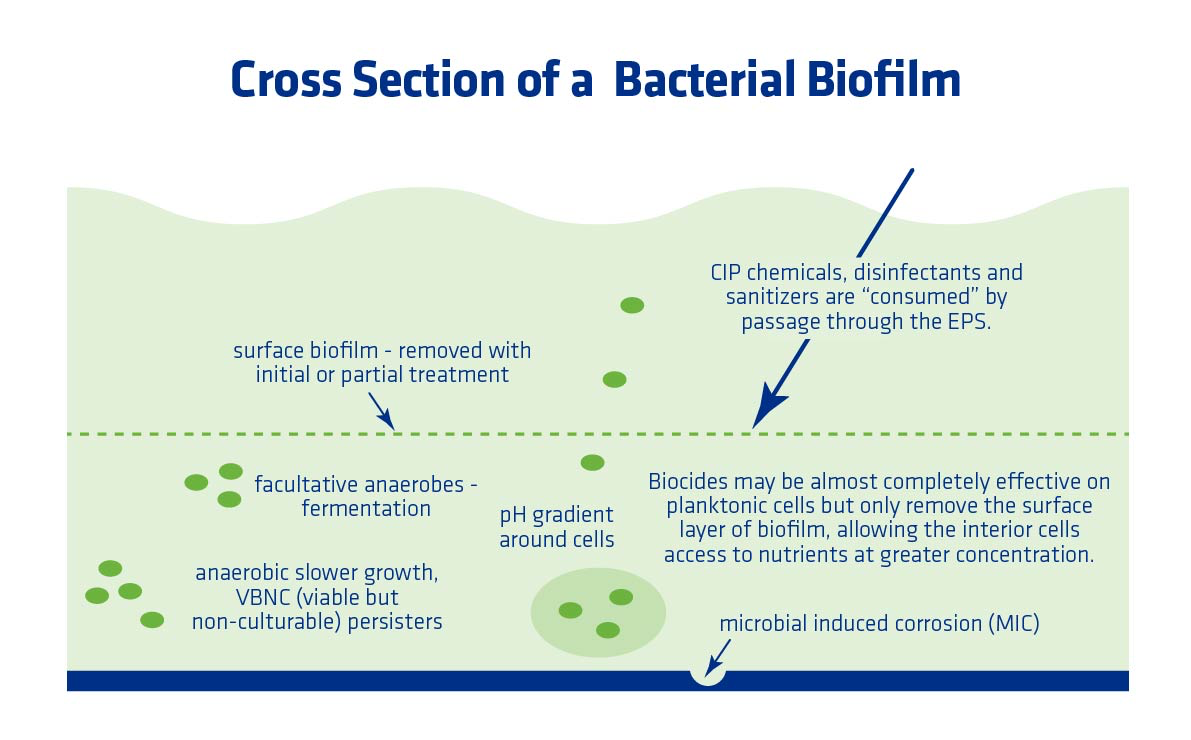
Location of Plant Biofilms
Biofilms can form on any surface that encourages bacterial growth and also in areas that might not have adequate agitation or fluid movement. Some of these locations include mash coolers, props, fermenters, and pipes. Beerwells, in particular, can harbor biofilms because they are rarely emptied completely. Stillage, water recycle lines, and cooling towers can be areas of concern as well.
There are two process indicators that can help plants identify the presence of a biofilm in heat exchangers:
- Incoming and outgoing heat exchanger temperatures can be used to calculate a temperature differential (often known as ∆T). A drop in ∆T indicates reduced exchanger efficiency due to fouling or biofilms.
- Increased incoming heat exchanger pressure can also indicate a decrease in efficiency and presence of a biofilm.
For tanks and non-heat transfer equipment, visual inspections and/or periodic shutdowns are recommended. Borescoping is a great and less intrusive way to inspect equipment.
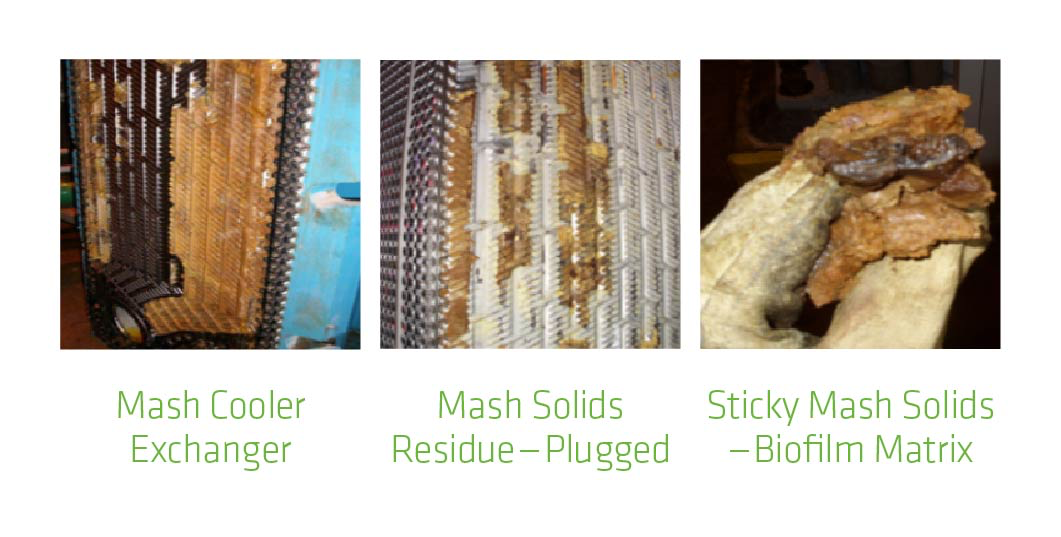
Cleaning is the most effective defense against bacterial infection. Keeping a plant clean will reduce the amount of antibiotics needed to control infection. In fact, using only antimicrobials without cleaning is not recommended because it is not economically feasible or effective.
The 4 T’s of CIP – Critical Parameters
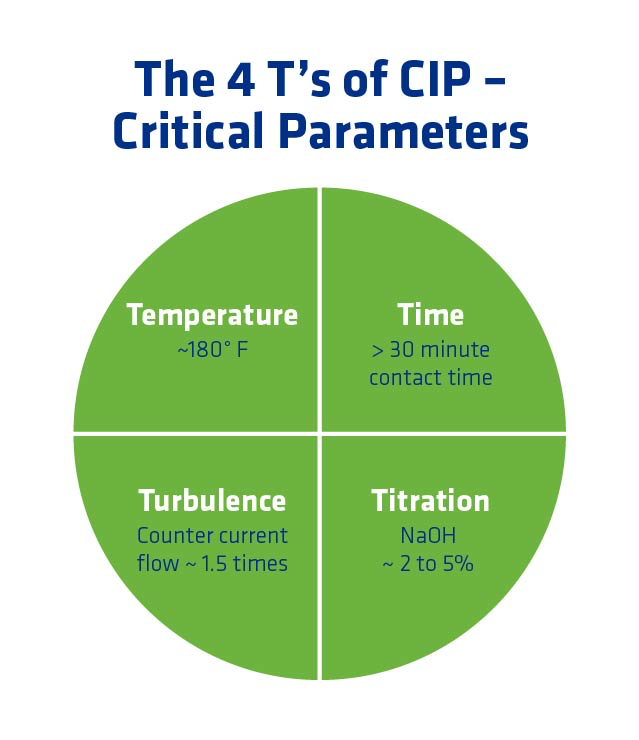
Effective CIP is achieved by following the Four T’s:
- Temperature: Temps above 180°F are best for killing bacteria and for effective chemical penetration.
- Time: The more time chemicals are in contact with bacteria and mash solids, the more effective the removal.
- Titration: Keeping the true caustic strength in a range of 2-5% is most effective for removing bacteria and organics.
- Turbulence: Counter current flow is ideal for generating the necessary turbulence to remove biofilms and other difficult to remove organics. If counter current flow is not possible, 1.5 times the normal flow rate should be the CIP supply velocity target.
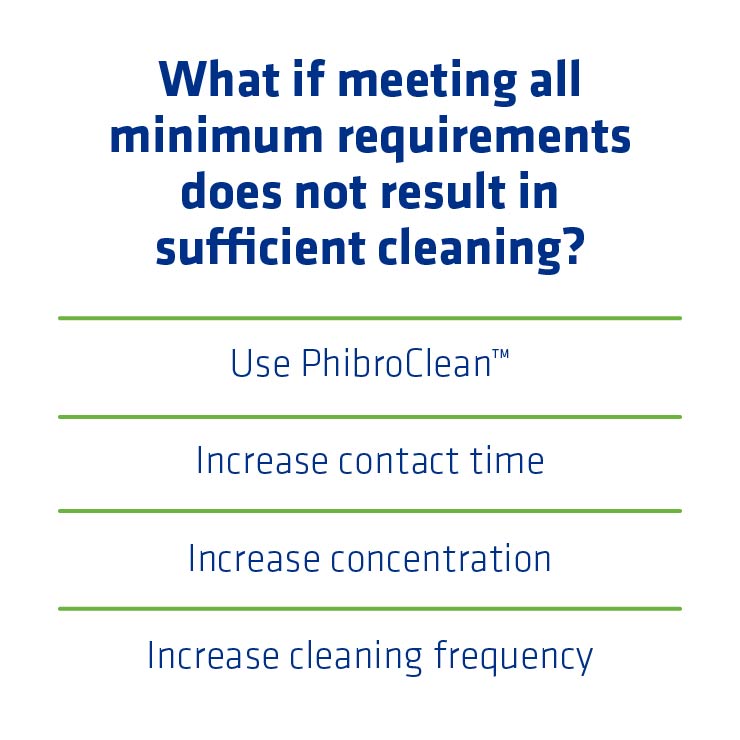
Using an additive like PhibroClean, will improve the cleaning of caustic CIP at lower concentrations. This can help improve plant cleanliness and reduce costs by reducing the amount of caustic needed.
Strategies to improve cleaning effectiveness if bacterial growth is still occurring in the plant include the steps listed in Figure 7.
One quick way to determine how changes in CIP procedures have impacted the cleanliness of the plant is to perform a benchtop incubation. The benchtop incubation procedure involves the following steps:
- Collect mash sample and analyze with HPLC. Allow sample to “incubate” for 24 hours and analyze again with HPLC. Whether or not there is any increase in organic acids and the magnitude of the increase indicates cleanliness of the sample.
- It is recommended that plants pull and analyze a sample from the same location before and after CIP for the best determination of cleaning effectiveness.
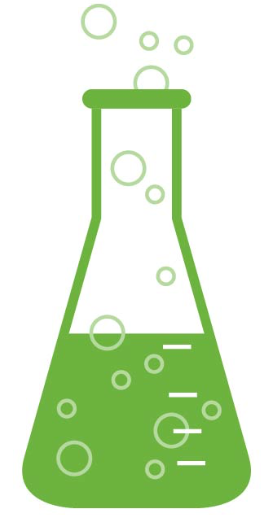
Fouling in Ethanol Plants
There are many different types of fouling that can occur in ethanol plants. It’s important to know how to identify each because they require different cleaning solutions. Fouling can generally be categorized as one of the following:
- Scaling: Insoluble organic deposits
- Biofouling: Colonies of bacteria and biofilms
- Composite Fouling: Organic and inorganic combinations
- Chemical Reactions: By-products in a system to form polymers, from heat to pH, burned sugar or proteins
- Corrosion: Growth of corrosion deposits

Choosing the Right Cleaning Solution
Once a plant determines where fouling is occurring and what is causing it, the most appropriate product can be selected for targeted application.
Advantages of Caustic-Based Cleaners
- Excellent detergency properties when “formulated” (i.e. PhibroClean™)
- Effective disinfection properties, especially when used hot
- Effective at removing proteins and organic compounds
- More effective than acid in high organic environments
- Cost effective
Advantages of Acid Cleaners
- Effective on Calcium and Magnesium Oxalate (“beerstone”)
- Effective on Calcium and Magnesium Phytate
- Effective on Struvite
- Not degraded by CO2
The PhibroAC™ Acid Detergent Cleaner system
- Improves penetration into deposit layers
- Increases physical cleaving of deposits
- Enhances cleaning performance by removing inorganic components of fouling
One Phibro customer reported fewer plugged evaporator tubes and scale that was much easier to remove because of the use of Phibro AC in the plant. See figures below that illustrate this significant improvement.
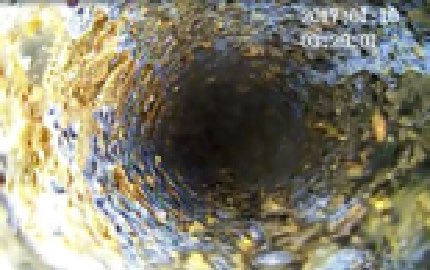
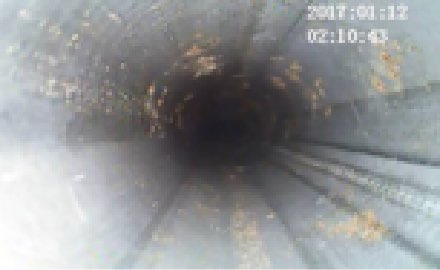
Advantages of Cleaning
In summary, clean plants run more efficiently and keep energy inputs in check.
Specifically, the operational advantages to proper cleaning include:
Mash Banks
- Lower infection rates
- Better heat transfer
- Extended periods between cleaning
Processing Lines
- Lower infection rates
- Higher throughput
Evaporators and Distillation
- Lower energy input (less steam)
- Higher throughput
- Less hydroblasting events
Oil System
- Higher oil production
- Lower frequency of cleaning events
- More production run time